Цементтэй карбид нь вакуум, Никель, Никель, Никель, Молидден, Молибден нь өндөр хатуулаг, Молидден, Молибден нь өндөр хатуулаг, СЭТГЭЛ бол Кемент Карбидын маш чухал алхам юм. SO-SNENTING нь нунтаг авсаархан нь нунтаг авсаарханийг тодорхой температурт халаана, үүнийг тодорхой хугацаанд хадгалахын тулд үүнийг авахын тулд үүнийг хөрвүүлэхийн тулд үүнийг хөргөнө үү. Цементийн карбидын үйл явц нь маш төвөгтэй бөгөөд хэрэв та болгоомжтой хандахгүй бол сэвсгэр хог хаягдал гаргахад хялбар байдаг. Өнөөдөр Zhuzhou chuangrui цементэн цементтэй Карбидын Co.
1. Карбидын суудаг хог хаягдал нь хамгийн түрүүнд хальслах явдал юм
Энэ бол Хөндлөнгийн гадаргуу, бүрхүүлийн гадаргуу нь ирмэгийн гадаргуу, бүрхүүл, хагарал, хэлбэрийн хагарал, Хальс нь ихэвчлэн COBALT-ийн контакттай холбоо барих нөлөөнд автдаг, ингэснээр нүүрстөрөгчийн соёолж, нягтаршлын хүч чадал буурч, авсаархан хүч чадал буурч байна.
2. Хоёр дахь хамгийн түгээмэл цементтэй карбид суулга суулга
40 микроноос дээш хавтанг нүх гэж нэрлэдэг. Цэврүүтэх хүчин зүйлүүд нь нүх үүсгэж болзошгүй хүчин зүйлүүд. Нэмж хэлэхэд "Сэтгэл хөдлөм," дарамттай металлууд, эсвэл суулгаагүй, эсвэл суулгасан биед бохирдсон биед норгог нь хатуу үе шаттай, шингэний үе шатууд нь наалдаж, шингэний үе шатууд нь наалдаж болно.
3. Гурав дахь хамгийн түгээмэл цементтэй Карбид суулга саатсан хаягдал бүтээгдэхүүн нь цэврүү юм
Цементийн карбидын хайлшны хайлшийн нүхэнд цооролт байдаг бөгөөд гүдгэр муруй гадаргуу нь холбогдох хэсгүүдийн гадаргуу дээр гарч ирнэ. Энэ үзэгдлийг цэврүүлэх гэж нэрлэдэг. Цэврүүтэх гол шалтгаан нь суулгацтай бие махбодь харьцангуй төвлөрсөн хийтэй байдаг. Ихэвчлэн хоёр төрөл байдаг: нэг нь сийлбэртэй биед хуримтлагдаж, суулгасан, суулгасан байдал, суудлын явцад агаар нь гадаргуугаас гадаргуу дээр шилждэг. Хэрэв Stoy Scraps, төмөр хаягдал, кобальт хаягдал, кобальт хаягдал, кобальт хаягдал, агаарт байх болно. Сэрүүлэгдсэн бие нь шингэн үе шатанд гарч ирнэ. Цэврүү нь хамгийн бага гадаргуу дээр хэлбэртэй байдаг.
Хоёр дахь нь суулгасан биед их хэмжээний хий үүсгэдэг химийн урвал байдаг. Сүлжсэн биед зарим испани орчим, шингэн үе шат хийсний дараа бензин үүсгэдэг, энэ нь бүтээгдэхүүний хөөсийг үүсгэх болно; WC-CO-COLOYS нь ерөнхийдөө холимог дахь ислийн боолуудаас үүдэлтэй байдаг.
4. Мөн тэгш бус байгууллага байдаг: холих
5. Тэгээд дараа нь хэв гажилт байдаг
Сүлжсэн биеийн өөрчлөлтийг жигд бус хэлбэр нь хэв гажилт гэж нэрлэдэг. Хэв гажилтын гол шалтгаан нь дараахь зүйлүүд байна Сэвсгэр бие нь нүүрстөрөгчийн орон нутагт маш их дутагдалтай байдаг тул нүүрстөрөгч нь шингэн үе шатыг харьцангуй бууруулдаг; Завины ачаалал нь үндэслэлгүй; Нөөцлөлтийн хавтан тэгш бус байна.
6. Хар зүрх
Халуу хугарлын гадаргуу дээрх сул талбай нь хар төв гэж нэрлэдэг. Гол шалтгаанууд: Нүүрстөрөгчийн агууламж, бага зэрэг бага нүүрстөрөгчийн агууламжтай. Согтоолгүй нүүрстөрөгчийн агууламжид нөлөөлдөг бүх хүчин зүйлүүд нь хар зүрх сэтгэл үүсэхэд нөлөөлнө.
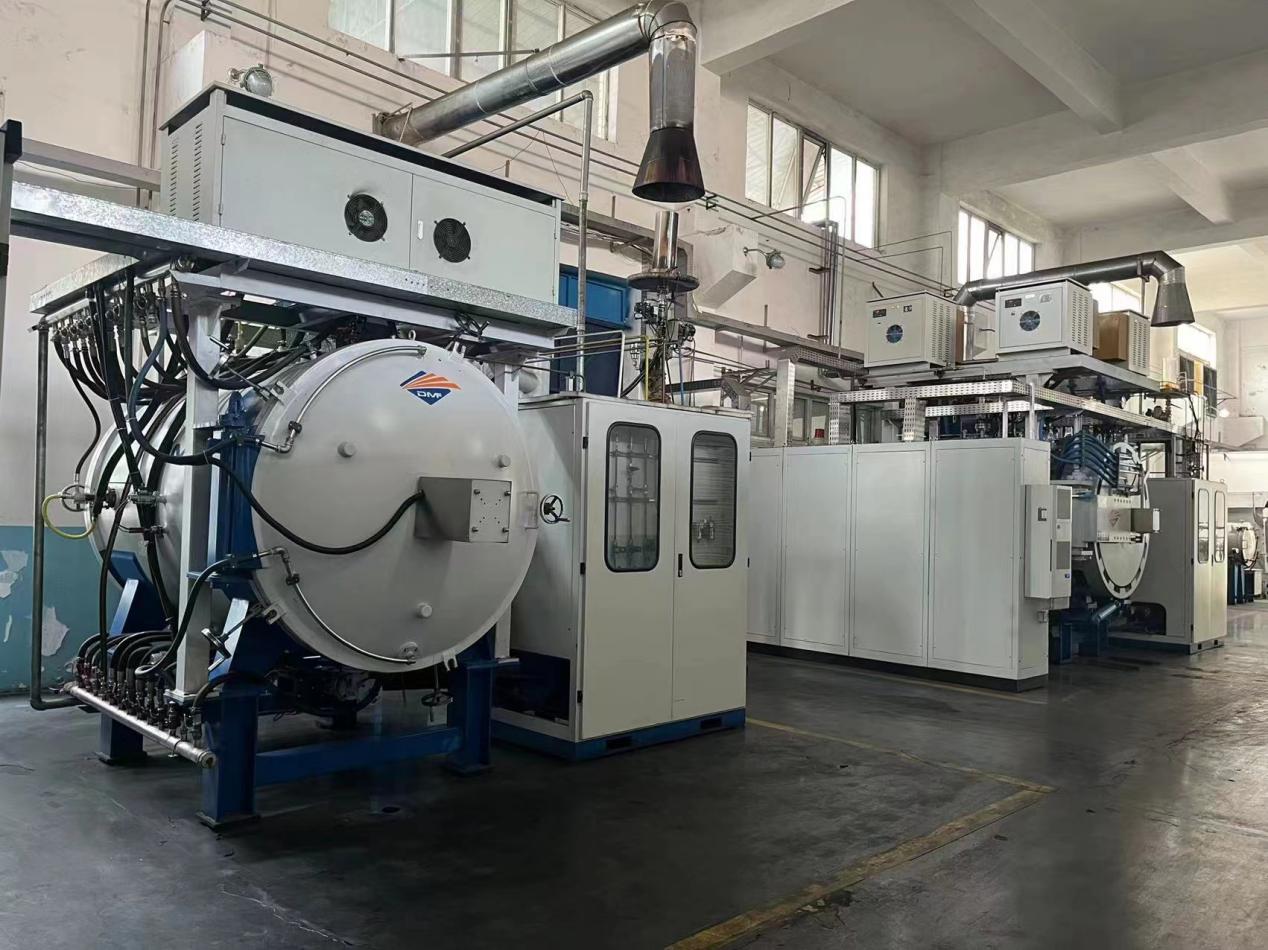
7. Хагарал нь цементийн карбидын соёолж буй карбидыг саатуулдаг
Шахалтын хагарал: Учир нь даралт нь дарамт шахалт нь сэвсгэр, уян хатан байдал нь суудлын үеэр илүү хурдан харагддаггүй. Исэлдэлтийн хагарал: Хатуу нь хуурай болтол нь хэсэгчлэн исэлддэг тул исэлдэлттэй хэсэг нь exidized хэсэг нь бүтэцгүй хэсгүүдээс ялгаатай.
8. Хэт их хүчээр
Стернинг температур хэт өндөр эсвэл барих хугацаа хэт урт байвал бүтээгдэхүүн хэт их шатах болно. Бүтээгдэхүүнийг хэт шатаах нь үр тариаг илүү зузаан болгодог, нүх нь нэмэгддэг. Дутагсан бүтээгдэхүүний металл бүтээгдэхүүний тууралт нь тодорхой биш бөгөөд энэ нь зөвхөн дахин халах хэрэгтэй.
Шуудангийн цаг: 1-р сарын 25-2024